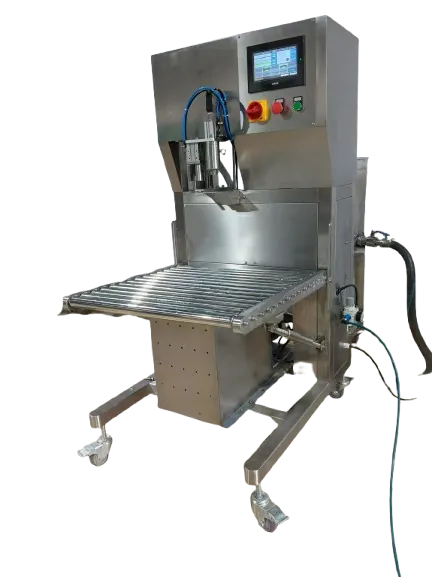
Bag-in-Box (BIB) & Stand Up Pouch (SUP) Filling Machines
zhangrenfangShare
The FenDa Bag-in-Box (BIB) & Stand Up Pouch (SUP) Filling Machines are advanced, versatile solutions designed for precision filling of thick and viscous liquids into two popular flexible packaging formats: Bag-in-Box and Stand Up Pouches. Engineered for efficiency and accuracy, these machines utilize weight-based filling technology with intelligent weighing systems and premium pumps, ensuring ±1% filling precision. Ideal for food, daily chemicals, industrial, and pharmaceutical industries, they handle a wide range of products—from purees and sauces to pastes and lotions—making them the perfect choice for modern, flexible production lines.

Key Features
Dual Packaging Compatibility
- Bag-in-Box (BIB): Optimized for large-volume packaging, ideal for cost-effective storage and transportation of products like purees, dairy, condiments, and industrial pastes. Pre-vacuuming technology ensures air-free packaging, extending shelf life.
- Stand Up Pouch (SUP): Designed for retail-ready, portable packaging. Supports stand-up pouches with spouts or zippers, suitable for snacks, beverages, personal care products, and more. Equipped with precise pouch positioning and sealing systems for secure, leak-free packaging.
Precision Weight-Based Filling
- Advanced Technology: Combines rotor pumps, high-accuracy weight sensors, and intelligent weighing modules to monitor filling in real time, ensuring consistent ±1% accuracy for both BIB and SUP formats.
- Stable Performance: Handles nectar-thick to honey-thick viscosities with equal precision, minimizing product waste and ensuring uniform quality.
High-Speed Efficiency
- BIB Capacity: Up to 220 bags/hour (water-based), maximizing large-scale production output.
- SUP Adaptability: Adjustable speeds to match pouch size and product viscosity, with rates up to 200 pouches/hour for retail-oriented packaging.
Fully Automated Operation
-
Seamless Process:
- BIB: Automatic bag locking, cap removal, pre-vacuuming, filling, and recapping.
- SUP: Pouch feeding, spout alignment, filling, and heat-sealing (or pressure-sealing for spouted pouches), ensuring minimal manual intervention.
- User-Friendly: Simple HMI interface; operators only need to load packaging materials, set parameters, and start—no complex manual adjustments required.
Durable & Hygienic Design
- Premium Materials: Constructed with food-grade stainless steel (AISI 304/316) and corrosion-resistant components to maintain product integrity and comply with global safety standards (FDA, CE).
- Easy Maintenance: Quick-release parts and smooth surfaces enable effortless cleaning, reducing downtime and ensuring hygienic operations.
Customizable Solutions
- Flexible Configurations: Available with single or double filling heads to match production demands.
- Tailored Options: Compatible with multiple pump types (rotor, piston) and additional modules (flowmeters, metal detectors) for specialized applications. Rotor pumps excel in handling viscous liquids with particles, while piston pumps offer versatility for semi-viscous products.
Technical Specifications
Parameter | BIB Filling | SUP Filling |
---|---|---|
Filling Range | 1–30 kg | 0.1–5 kg |
Filling Precision | ±1% | ±1% |
Max Speed (Water-Based) | 220 bags/hour | 150–200 pouches/hour |
Material Viscosity | Nectar to honey-thick | Low to high viscosity |
Operating Pressure | 0.5–0.6 MPa | 0.5–0.6 MPa |
Supply Voltage | AC220V/50Hz ±10% | AC220V/50Hz ±10% |
Air Consumption | ≥ 0.36 m³/min | ≥ 0.4 m³/min |
Filling Temperature | ≤ 95°C | ≤ 80°C (heat-sealing safe) |
Power per Head | 1.5 kW | 1.2 kW |
How It Works
Bag-in-Box (BIB) Process
- Bag Insertion: Place empty BIB into the spout holder.
-
Automatic Cycle:
- Machine locks the bag, removes the cap, and inserts the product valve.
- Pre-vacuum removes residual air to prevent oxidation.
- Rotor pump dispenses product until the target weight (monitored by weight sensors) is reached.
- Sealing & Ejection: Bag is recapped, and the filled BIB is released for boxing.
Stand Up Pouch (SUP) Process
- Pouch Loading: Position empty SUP on the conveyor or holder.
-
Automatic Cycle:
- Pouch is opened and aligned by mechanical grippers.
- Filling nozzle inserts into the pouch (or spout), and product is dispensed via weight-controlled pumping.
- After filling, the pouch is heat-sealed (or spout is capped) and ejected to the output conveyor.
Applications
Food Industry
- BIB: Purees, ketchup, condensed milk, cheese sauce, mayonnaise, yogurt, liquid eggs, soft ice cream.
- SUP: Snack sauces, honey, nut butter, liquid seasonings, single-serve beverages, cooking oils.
Non-Food Industry
- BIB: Industrial pastes, lubricants, chemicals, construction adhesives.
- SUP: Laundry detergents, shampoos, body lotions, automotive fluids, agricultural concentrates.
Why Choose FenDa Filling Machines?
- Cost Efficiency: Reduces packaging, storage, and logistics costs by 80–90% compared to rigid containers.
- Quality Assurance: Pre-vacuum (BIB) and air-tight sealing (SUP) protect product integrity and extend shelf life.
- Adaptability: Quick changeover between BIB and SUP formats with minimal downtime (5–45 minutes), ideal for multi-product lines.
- Reliability: Low maintenance, durable construction, and proven performance for 24/7 operations.
- Global Compliance: Meets strict hygiene and safety standards for food, pharmaceutical, and industrial applications.
Conclusion
The FenDa Bag-in-Box & Stand Up Pouch Filling Machines deliver unmatched precision, speed, and flexibility for modern packaging needs. Whether you require large-volume BIB solutions for industrial products or retail-ready SUP packaging for consumer goods, our machines ensure seamless operations and superior results. Upgrade your production line today with a solution designed for the future of flexible packaging.
Contact us to customize your ideal filling system!
Additional Notes:
- Sustainability: BIB packaging uses 80–90% less plastic than rigid containers and is fully recyclable. SUP designs can incorporate plant-based materials for eco-friendly options.
- Heat Filling: Optional buffer tanks enable hot filling (≤95°C for BIB, ≤80°C for SUP) with anti-foam control.
- SMED Compliance: Fast changeover technology reduces downtime, aligning with Single-Minute Exchange of Die (SMED) principles.